How to Optimize Product Growth & Maturity with Siemens Teamcenter
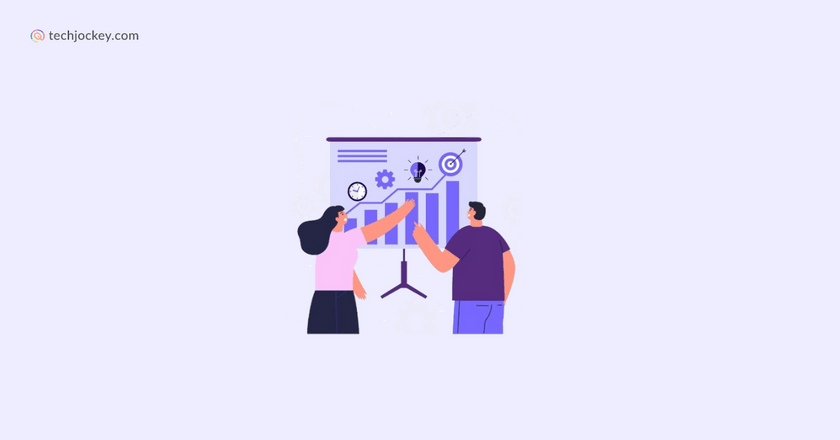
Summary: Optimizing product led growth and maturity with PLM software is essential for businesses to stay competitive. The software streamlines workflows, reduces costs, and enhances collaboration. Tools like Siemens Teamcenter provide fast access to resources that fuel efficiency and innovation.
In today’s fast-paced business world, managing product growth and maturity is key to staying competitive. Product Lifecycle Management (PLM) is a vital strategy that oversees every stage of a product’s journey, from the initial concept to reaching maturity in the market.
As products mature, it becomes crucial to optimize supply chains and workflows to meet sales targets and align with business strategies. Understanding the product lifecycle helps managers make informed decisions and lead their teams effectively.
For production optimization, companies need to streamline their processes and adapt to changing market needs. By using PLM team center effectively, businesses can ensure their products meet customer demands and stay relevant in the market. Read on to explore how to make the most of PLM to drive production optimization.
What is Product Lifecycle Management?
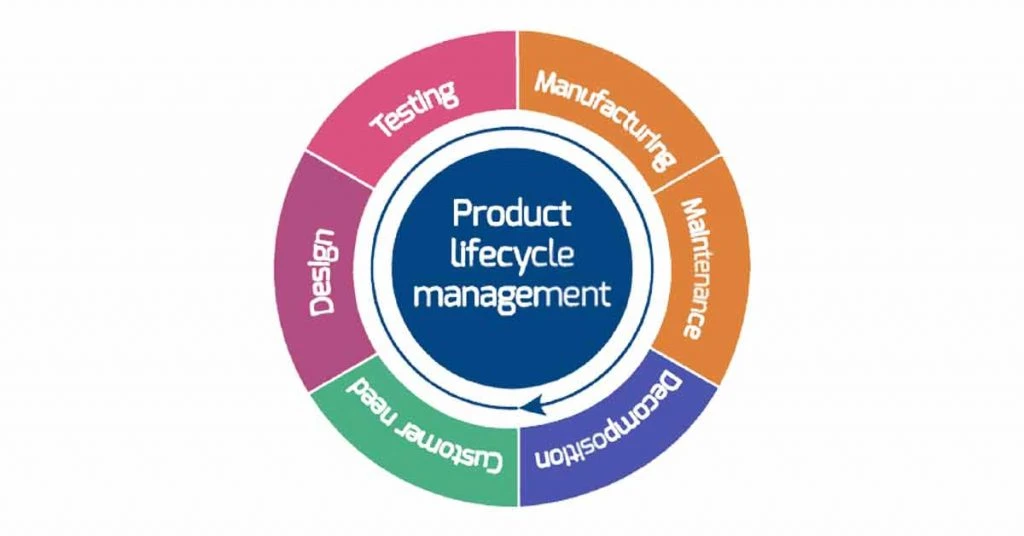
Product lifecycle management is a comprehensive process overseeing the evolution of a product from its conceptualization to its full maturity. It involves managing various aspects including design, manufacturing, production, promotion, modifications, and so on.
PLM aims to connect and organize different stakeholders involved in product development, thus enhancing efficiency and establishing a structured process for bringing ideas to market.
The primary objective of PLM is to ensure that each product developed by a company achieves optimal level of quality, economic viability, and buyer’s impact. This entails several key functions:
- Managing product-related documentation such as design drawings and bill of materials
- Handling project data as well as electronic documents
- Identifying and optimizing workflows
- Assigning tasks to teammates
- Limiting access to certain product details for specific individuals
How Siemens Teamcenter Help Optimize Product Growth & Maturity?
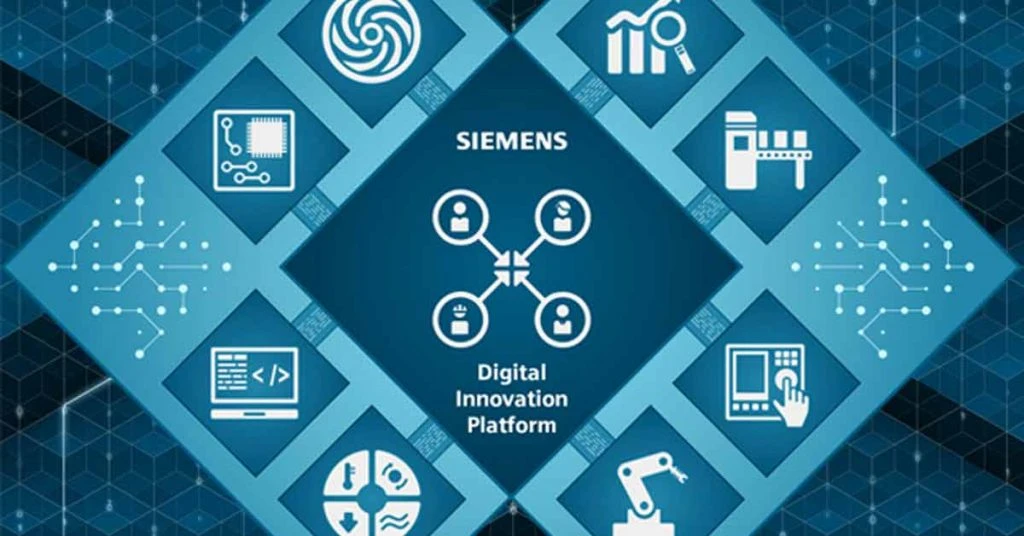
Siemens Teamcentre software helps in product optimisation across various industries. Its multifaceted functionalities cover crucial aspects of product development, from conception to market launch and beyond.
Below we have attempted to define optimization techniques and illustrate how it contributes to product evolution and drives competitiveness in the market.
1. Community Collaboration: Teamcenter fosters community collaboration by providing a secure and adaptable environment where distributed multi-disciplinary teams can work together in real-time.
This collaboration extends to suppliers, partners, and customers, facilitating concept studies, program reviews, design assessments, and engineering change evaluations. Key capabilities include;
- Virtual teaming for quick establishment and expansion of virtual teams
- Virtual conferencing for easy sharing of information without travel
- Ad hoc knowledge capture for collecting and integrating unstructured knowledge
- Visual product data collaboration, allowing integrated visualization and analysis of data from various formats
- Personal portals tailored to individual roles, responsibilities, and security entitlements
- Synchronous and asynchronous collaboration features, including 3D visualizations, application sharing, instant messaging, and document sharing.
2. Systems Engineering and Requirements Management: Teamcenter supports systems engineering and requirements management, enabling the definition, capture, management, and leverage of product requirements. It ensures traceability, linking requirements to downstream processes for visibility and understanding.
Additionally, it facilitates systems architecture definition and extended application/systems integration, promoting seamless integration with critical systems and tools like Matlab/Simulink and Microsoft Office.
3. Lifecycle Visualization: Siemens Teamcenter offers a consistent and scalable lifecycle visualization backbone, enabling stakeholders to view products as they evolve in 2D and 3D formats. This capability allows for early stakeholder involvement, improved decision-making through visualization-based workflows, and streamlined innovation by facilitating virtual collaboration and prototyping.
4. Reporting and Analytics: This software provides real-time and near real-time reporting and analytics tools to establish, measure, and analyze key performance metrics across the product lifecycle. It offers powerful data aggregation, rich lifecycle reporting, multidimensional data views, and advanced analytics capabilities to optimize data analysis and decision-making processes.
5. Portfolio, Program, and Project Management: It supports collaborative portfolio management, program and project management, resource management, financial management, and business performance management.
These capabilities enable organizations to define portfolio strategies, plan and execute programs/projects, manage resources and finances effectively, and ensure business performance alignment with strategic goals.
6. Easier BOM Management: Teamcenter’s bill of materials (BOM) management capabilities provide total visibility into product definitions and evolution across the lifecycle. It supports product configuration, enterprise BOM management, process-specific data structure and management, lifecycle representation management, and context management for improved BOM accuracy and management efficiency.
7. Compliance Management: Siemens Teamcenter facilitates compliance management by documenting, enforcing, and tracking regulatory compliance throughout the product life cycle. It supports environmental compliance, medical compliance, export control, and document/records management, ensuring adherence to regulatory requirements and standards.
8. Supplier Relationship Management: This PLM software drives supplier management and strategic sourcing initiatives by transforming the way suppliers collaborate with product development and procurement teams.
It supports supplier identification, assessment, monitoring, quality management, joint project management, and performance monitoring, streamlining sourcing processes and enhancing supplier relationships.
9. Simulation Process Management: Enables early assessment of product performance and quality through simulation process management capabilities.
It supports simulation data management, change management, structure management, and visualization, facilitating collaboration and integration of simulation processes with the product life cycle.
10. Manufacturing Process Management: It supports comprehensive manufacturing process management, including BOM/BOP management, change management, resource management, and production/shop floor management.
It ensures the seamless integration of engineering and manufacturing teams, optimizing manufacturing processes and enhancing overall efficiency.
Conclusion
By utilizing Product Lifecycle Management Software businesses can effectively optimize product growth and maturity. This involves streamlining processes, reducing costs, improving product quality, and fostering collaboration, ultimately enabling companies to meet customer demands and remain competitive in the market.
Additionally, tools like Siemens Teamcenter further enhance efficiency and innovation by providing fast access to essential resources. With PLM software as their ally, businesses can confidently navigate the complexities of product development with confidence.
The Techjockey content team is a passionate group of writers and editors dedicated to helping businesses make informed software buying decisions. We have a deep understanding of the Indian software market and the challenges that businesses face when choosing the right software for their needs. We are committed... Read more